工場における安全対策やコロナ対策についてご紹介

2023/11/14 更新
技術の発展や従業員への注意喚起に伴い、昔に比べて工場における事故は減少しています。しかし、現在でも労働災害や死傷者がゼロになることはありません。工場はさまざまな機械が作動しており、重量があるものや化学物質を取り扱うことがあるので安全対策は必須です。そこで、工場で発生する事故の種類や工場における安全対策、コロナ対策についてご紹介します。
工場において安全対策が
重要視される理由
厚生労働省が公表した「令和2年の労働災害発生状況」によると、全業種の労働災害による死亡者数は年間802人でした。一昨年の死亡者数からは18%減、昨年の死亡者数からは5.1%減と減少しており、3年連続で過去最少となっています。
しかし、令和2年の休業4日以上の死傷者数は平成29年からは8.9%増、昨年からは4.4%増と平成14年以降で最多となっています。
出典:厚生労働省
国・事業者・労働者が労働災害を減少させるために重点的に取り組む事項を定めた「第13次労働災害防止計画」では、平成29年比で死亡者数を15%以上、死傷者数を5%以上減少させることを目標にしています。
業種別の労働災害発生状況をみると、陸上貨物運送事業、小売業、社会福祉施設及び飲食店で増加しており、製造業の死亡者数は2年連続で減少(前年比3.5%減)しています。しかし労働災害を減らすためにも、各企業における安全対策の強化が重要視されています。
工場で発生する事故の種類
工場で発生する事故にはさまざまなものがあります。ここでは 厚生労働省が公表した「令和2年の労働災害発生状況」の事故の型別労働災害発生状況をもとに、工場で発生しやすい3つの事故に注目してみました。
転倒事故

休業4日以上の死傷者数の原因として最も多かったのが転倒によるものでした。全体の24%を占めるなど大きな割合となっています。
転倒の原因として、よそ見をして歩く、工場の中を走るなど従業員本人によるものが考えられます。しかし、床の材質が滑りやすい、清掃が行き届いていないなど管理者側の責任によるものも原因となりかねません。転倒事故は軽い怪我で済むこともありますが、打ちどころが悪いと重大な事故に繋がる危険性を含んでいます。
巻き込まれや切断事故

死亡者数の16%、休業4日以上の死傷者数で10%を占めたのが、はさまれ・巻き込まれによるものでした。はさまれ事故とは固定部分と可動部分または可動部分同士の間に身体の一部がはさまれる事故です。巻き込まれ事故とは、作業中や清掃中に衣服や身体の一部が機械に巻き込まれることによって起こります。
切断事故は、鋭利な機械を使った作業中に手指が切断される、稼働中の機械の近くにいるときに転倒や転落することによって身体が接触することなどで起こります。近年ではクリーニング工場の脱水機で首が切断されるという痛ましい死亡事故も起きました。従業員自身が機械内に身体を入れたことも考えられますが、安全装置機能の不備や安全管理体制の不備も原因として考えられます。
転落事故

死亡者数の24%、休業4日以上の死傷者数で16%を占めたのが墜落・転落によるものでした。工場は職場内に段差が多いことやハシゴや脚立を使った作業、高所での作業が多いことから墜落・転落事故が起こりやすくなります。正しいハシゴや脚立の使い方をする、安全帯をつけるなどで事故の防止ができるので、企業側は従業員に徹底したルール順守を行わなければなりません。
工場における安全対策
工場での事故を減らすためには安全対策が重要です。安全対策のルールを作るだけに留まらず、徹底した職場環境づくりや従業員教育などルール順守のためのポイントについてご紹介します。
5Sを徹底する

5Sとは、職場環境や安全対策を改善するための考え方やスローガンです。「整理・整頓・清掃・清潔・しつけ」をローマ字表記としたときに、全てにSがつくので5Sと呼んでいます。5Sについて細かくチェックしてみましょう。
・整理
まずは職場内が整理されていることが大切です。さまざまなものを扱うときに、不要なものを放置しておくと職場環境が悪化するだけではなく衛生的にも問題が発生します。事故の原因となりかねない転倒を防ぐこともできるので、普段から必要なものと不要なものを区別することが大切です。
・整頓
ものが散らかっていると危険要素に気づきにくくなります。普段から資材や道具の置き方や個数が決まっていれば、不要なものやなくなったものに気づきやすくなるでしょう。
業務が効率化されるだけではなく、紛失物の早期発見や混入事故の防止にもつながります。
・清掃
職場の清掃で転倒や転落を防ぐだけではなく、環境や扱う物によっては、細菌や微生物の除去にも繋がります。また、機械をスムーズに動かすためにも定期的なメンテナンスは必要です。
・清潔
注意喚起のポスターの破れ、看板の汚れなどで、危険性が伝わらず事故につながる場合があります。また、床が汚れている、不要なものが落ちていることが原因で、転倒や転落に繋がることもあるでしょう。普段から清潔を保つことは安全対策にもなります。
・しつけ(教育)
従業員が整理整頓、清掃や清潔を意識するためにも、必要性や危険性を十分に説明する必要があります。ルールを守り習慣にするために、定期的にしつけをすることで事故が起こりにくい環境づくりがかないます。
定期的な従業員教育

5Sの徹底以外にも職場内では走らない、制服の裾はズボンに入れる、足元に物を置かないなどのルールを定期的に従業員に示す必要があります。基本的なことではありますが、慣れや気の緩みでついルールを破ってしまうこともあるので、定期的な注意喚起が必要です。定期的に教育することは、危機感の共有だけではなく従業員へのルールの浸透にもつながります。
定期的な設備保全やチェックリストの浸透

機械の経年劣化などによって、安全性に問題が発生することがあります。保全計画をもとに機械や設備の点検・修理、部品交換を定期的に行いましょう。従業員が機械のチェックを徹底することで事故は防げます。必要なチェックリストは昔からのものを使い続けるのではなく、状況や業務内容に応じて常にアップデートすることが大切です。また、チェックリストは従業員同士で共有することで、事故防止の意識が高まります。
工場でのコロナ対策
新型コロナウイルスの感染拡大によって、工場でのコロナ対策も欠かせないものになりました。従業員の健康や暮らしを守るためにも工場でのコロナ対策も徹底しましょう。
動線の重複を避け、消毒の徹底
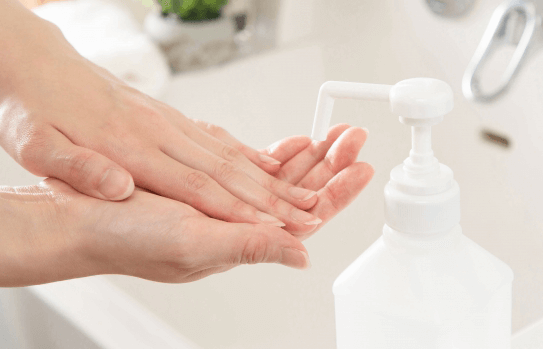
同一箇所に多くの人が集まると感染リスクが高まります。時差出勤や休憩時間をずらすことによる対策が必要です。更衣室や休憩室の入室人数を決めるなどの対策も効果的といえるでしょう。また、工場内に入るときは付着した細菌・ウイルスの侵入を防ぐために洗浄・殺菌のルール作りを行うなど消毒の徹底も必要です。
定期的な換気や一定の距離の確保

換気が可能な場所においては、常に換気を心掛けるか1時間に2回以上窓を開けるなどの対策が必要です。また、従業員同士の距離は2メートルを目安に保つ必要があります。従業員同士の間隔が狭いときは、作業空間や人員配置の見直しが必要です。
従業員の体温管理

新型コロナウイルスの感染発覚の目安として体温管理が重要です。出勤前に体温を確認する、勤務中に発熱した場合は直ちに帰宅させるなどの対策でほかの従業員への感染を防ぎます。新型コロナウイルスに感染していなくても、熱が出た状態で作業するのは危険なので、事故防止にもつながるでしょう。
まとめ
工場の安全対策が重要視される理由や事故の種類、安全対策の方法についてご紹介しました。近年は従来の安全対策だけではなく、新型コロナウイルスに対する対策も迫られています。企業側が安全対策に取り組むことは、労働災害や事故の頻度の低下や被害の最小化につながるでしょう。ご紹介した対策方法をもとに、ルールや管理体制の参考にしてください。